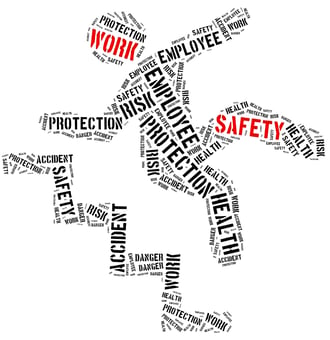
Here’s a shocking fact: At over 8 million visits per year, fall accidents account for 21.3% of emergency room visits. Slip and fall cases make up 1 million of those visits to the hospital every year.
These visits not only cause broken bones and sometimes even more serious injuries, but they also are the primary cause of lost days from work, as well as the leading cause of worker’s compensation claims.
And the majority of these slips and trips in the workplace come from unsafe, hazardous flooring. In fact, 55% of all slips, trips, and falls happen as a result of hazardous flooring, an easily preventable issue with the proper procedures in place.
Slip and fall cases cost businesses around $11 billion each year. Sure, it costs businesses money to defend these cases, but it also causes the injured person to miss work and potentially deal with the resulting lifelong injuries. What else should you know about slips, trips, and falls?
- The average slip-and-fall injury costs $20,000, but the cost for a business to defend a slip-and-fall case is around $50,000
- An employee who has been injured in a slip-and-fall incident misses, on average, 38 days of work
- Slips, trips, and falls account for 15% of all accidental deaths, second only to automobile accidents
In today’s world where every cent counts and every worker matters, businesses can’t afford not to take slips, trips, and falls seriously. Businesses then need to implement slip-resistant flooring, and also invest in portable, accurate, and easy-to-use handheld friction measurement tools, so they can be sure their floors are truly slip-resistant, and their employees are always safe.
Flooring Safety Standards
When a building is being constructed, materials are carefully chosen to provide a safe environment. Any flooring that is being used in the construction of a new building has been put through rigorous testing to make sure it is safe.
When this flooring is being tested for safety, evaluators are looking at the flooring’s coefficient of friction (COF) value. What does this mean?
- Coefficient of Friction The coefficient of friction (COF) is a mathematical term used to calculate the effect of one substance or item (a show, for example) over another item (in this case, the floor). It is a way to measure the ability of a surface to resist slipping or sliding. The coefficient value varies based on how "moveable" something is. For example, a tile floor covered in liquid from a spill will have a low coefficient of friction while tires on a tarred road will have a very high coefficient of friction.
OSHA has recommended that flooring has a COF value of at least 0.5. This number was not arbitrarily set in place, but is based upon a great deal of research. And this is not a standard for every floor across the board.
Some flooring needs to have a greater COF, in places where certain responsibilities put individuals at a higher risk of falling. This means that flooring needs to have a higher COF in places where individuals are carrying heavy items, pushing or pulling heavy objects, or walking up and down ramps.
Especially at entryways, in commercial kitchens, or anywhere a surface may become wet, there is a need for an even higher COF to prevent slipping as well.
Of course, when flooring is installed, building supervisors, architects, and safety consultants should always ensure that flooring meets these OSHA standards. However, after regular, daily wear and tear, maintenance, and cleaning, there’s a high likelihood that the slip resistance will wear away and become less safe.
So how can you be sure that your flooring continues to comply with OSHA’s standards, and will help keep your employees and visitors safe from slipping?
On-Site Friction Testing
Perhaps the best way to evaluate your flooring and know that it is up to OSHA’s standards? You should be using a handheld, portable friction analyzer on-site, to regularly test the COF values of your flooring, monitor the wear and tear, and avoid costly accidents.
Our friction test equipment, such as the portable friction meter, can be used by anyone to provide accurate COF data when testing the floor. The operator places the meter on the surface, ensuring the contact point of the meter is touching the floor, and presses a button. That’s it. Multiple measurements are stored within the meter and an average COF is calculated.
Because operation of the meter is so simple, there’s no variance in results between users. You can trust your results to be accurate, which means your test will always correctly indicate where you may need to improve your flooring’s slip resistance, either by replacing or resurfacing the flooring.
Preventing Falls
According to the Consumer Product Safety Commission (CPSC), floors and flooring materials are the cause of more than 2 million fall injuries every year. So how can you mitigate your risk for slip, trip, and fall accidents in your workplace? Here are three practices your company should follow:
- When choosing flooring for a space, consider how the day-to-day activities may affect slip resistance and the COF. Tile flooring is incredibly slippery when it is wet, and should be avoided anywhere that spills may frequently occur, or near entryways where moisture may be carried in. Also, smooth concrete, found in many garages, becomes dangerously slippery after the inclusion of the slightest bit of moisture. However, adding a slip-resistant coating to your floor can help increase the COF and prevent falls.
- Don’t ignore your flooring’s flaws. Over time, cracks and holes in your flooring materials can develop. These can quickly become safety hazards that put you and your employees at risk. Having a regular maintenance and repair schedule to address issues before they become a liability issue is vital to your building’s safety.
Additionally, it’s crucial to regularly test the changing COF of your flooring with a friction analysis meter to ensure your floor is still compliant with OSHA regulations - and still safe for your employees.
- Use floor coatings as a safety factor, not just for aesthetics. A glossy finish on a floor may have a beautiful effect, but is it really safe? Glossy flooring tends to become slippery and unsafe-especially if it gets wet. You don’t have to sacrifice form for function, though. Coatings can be strategically selected to provide the glossy aesthetic you want, while still having slip-resistant qualities to protect your employees.
Coating additives, such as aluminum oxide, increase the slip-resistance of a floor’s finish, and UV-cured coatings provide additional slip resistance on polished concrete and similar surfaces. You should always choose your employees’ safety above anything else, but fortunately, advances in flooring materials mean you can choose a stunning design still, too.
Slips, trips, and falls are the most common accidents in the workplace. Regular testing of your flooring with a friction analysis meter and careful maintenance can help you prevent these easily avoidable, unfortunate accidents. Using a friction analysis meter will provide you with a safer work environment and hopefully, many fewer employee slip, trip, and fall incidents. Your team encounters less risk of falls, and your workplace is a safe space. Not only does this keep you in compliance with OSHA standards, but it can help you avoid costly injury-related expenses too.
To find out how our portable handheld friction meter can help your company ensure the integrity of the surfaces throughout your facility, please download our friction analysis tip sheet today.